Hotcleat® - magnetic conveyor belts for mobile installations
Hotcleat® Magnetic conveyor belts are deployed in machine factories or end users. A Hotcleat® Magnetic conveyor belt separates high volumes of iron or steel (various metals), or ferrous parts, from raw materials quickly and effectively and discharges these metals automatically and continuously. Through an overhead belt magnet. In the case of mobile installations, >90% of the magnetic belt hangs transversely on a flat, profiled or conveyor belt with carriers. This can be either flat or in a trough. The aim is to remove undesirable metal particles for the cleanest possible end product or for further processing so that nothing is damaged on machines further down the line.
An overhead magnet has a drive and reversing drum including a frame. The frame then contains the magnetic core that attracts the material. Near the core, the material is attracted (this is where the forces are strongest). The moment the material reaches the drive or reverse roller using the Hotcleat® flights, the force of the magnetic core decreases to such an extent that, in combination with the belt speed and flights, the material is released. This is then discarded sideways. In this way, the metals are separated from the remaining material.
The conveyor belt made of highly abrasion-resistant rubber is fitted with carriers. To ensure that the metal parts are captured properly, our Hotcleat® carriers are hot vulcanised on the Probelt® base belt. It is often the case that too small drum diameters make great demands on a base belt, so not all belts are suitable for a top belt magnet. The right and unique composition of the base belts and technical know-how is important to deal with the often common small drum diameters. There is also a high belt speed which exerts an additional load on the weld, making correct welding techniques and monitoring of this crucial. In addition, our Hotcleat® cleats are made of unique compounds that ensure, for example, stable cleats. Tear-resistant, abrasion-resistant, etc. This is also because these are often sharp and abrasive pieces of metal that can quickly damage the belt and cleats when configured incorrectly. The de-icing efficiency of top band magnets ranges from 70% to 90%. This varies depending on the magnet design, product flow and placement. It is a reliable and effective method of separating large quantities of iron. This method of separation prevents machines such as shredders from being damaged by iron particles.
The technical complexity of overhead magnets for mobile plants is well known to our specialists. We combine our knowledge and experience of applications in various industries from Recycling, Agro and Food. We like to think along with our customers, even if the solution is completely new.
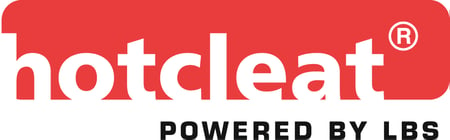
ungeplanned stop?
Next day deleivery optional
key benefits Hotcleat® Magnetic conveyor belts for mobile installations
Key-Benefits (USP's) Hotcleat® magnetic conveyor belts:
- » No detached cleats
- due to poor bonding of cleats
- due to weather / temperature & product influences - » Less sensitive to smaller pulley diameters
Limited width cleatbase (vs glued) results in less tension at the pulleys and less power consumption - » Improved working life of the cleats
- » Environmentally friendly
- no use of industrial glues needed/neccesary - » Cost saving for end-user
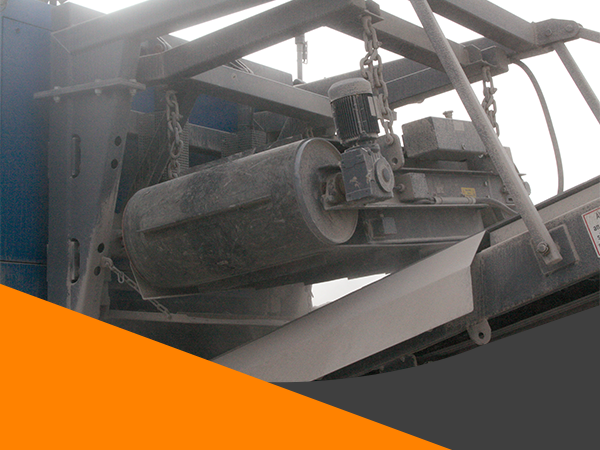
Solutions for Mobile installations
» Pulverising and/or shredding
» Screening
» Separation
» Transport
Fields of application for mobile plants
» Composting
» Household waste
» Wood
» Stone & building rubble
» Residual waste
» Metal
» Etc..
benefits Anti-magnetic mechanical fasteners
The method of making the conveyor belt for overbelt magnets endless is also an important aspect for the quality of the conveyor belt. What does it mean to choose anti-magnetic mechanical fasteners compared to an endless hot vulcanized joint?
The advantages of these fastener are:
- » Faster replaceable; this is because the tendon can be removed from the connector quickly and easily. This allows the conveyor belt to come off quickly. By just turning back the span of the drums, the new conveyor belt fits easily around the installation. When the new strap is on it, the tendon can go through the connector and the strap can be tensioned.
- » Less production loss, this is because the conveyor belt can be replaced quickly and the machine is stopped for a short time.
The main difference between a connector and a hot vulcanized joint is that you do not need to (partially) disassemble your overbelt magnet installation to fit your endless hot vulcanized conveyor belt. Especially on location without access to proper equipment.
It is very important to choose a completely anti-magnetic mechanical fastener. This is because otherwise the mechanical fastener can be attracted to the magnet and cause damage to the installation. Additionally small parts can “stick” to the mechnical fastener which can result in a broken mechanical fastener over a period of time due to wear and tear.
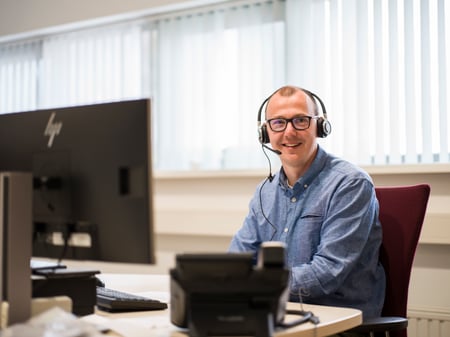
STAY UP-TO-DATE
Always be informed of our latest news? Sign up now for our newsletter, via the bar below.